膜电极(MEA)是氢燃料电池和PEM制氢电解槽的核心部件,是电化学反应的关键部件,其结构组成主要有质子交换膜、催化剂层、气体扩散层、边框膜等。
目前常见的膜电极生产流程主要涉及催化剂浆料制备、涂布质子膜形成CCM、热压气体扩散层、贴合边框膜等工序。
其中,膜电极催化剂层的涂布工艺可以有很多种,常见的有热转印、直涂等。
一、热转印
热转印过程涉及将催化剂油墨或粉末预先涂布或印刷到一个可转移的基材(通常是高温下稳定的薄膜)上,然后通过热压过程将催化剂从转移膜转移到质子交换膜或气体扩散层上。
制备步骤:
1.催化剂油墨的制备:首先,将催化剂粉末与适当的溶剂和粘合剂混合,制备成催化剂油墨。这一步骤类似于其他涂布法中催化剂溶液的制备。
2.催化剂的涂布:将催化剂油墨涂布或印刷到一个具有良好热稳定性的转移膜上。这个转移膜需要在后续的热压过程中保持完整,同时能够在适当的温度下释放催化剂。
3.热压转移:将含有催化剂的转移膜与质子交换膜或气体扩散层叠加在一起,并在热压机中加热压合。在此过程中,催化剂从转移膜转移到目标基底上。
4.转移膜的移除:在催化剂转移完成并冷却后,移除转移膜,留下催化剂层紧密地附着在PEM或GDL上。
热转印优势与不足:
1.可以精确控制催化剂的形状和大小:通过数字化设计,可以精细定制不同形状和尺寸的催化剂并将其完整地转移至电极表面上,有利于提高电化学反应的效率和选择性;
2.制备工艺更加精密:将催化剂转印到电极表面上,可以在较小的区域内形成极薄且高度一致的催化剂层。对于微观尺度下的反应表面和形貌控制更高;
3.可以实现多层催化剂堆叠:可以将多种催化剂顺序转移至电极表面上以提高复合催化效率;又可减少外界干扰、如温度等因素影响,还可以方便地通过选择性去除,避免环境污染等问题。
不过,热转印法在大批量生产上,存在效率需要进一步提高的问题。
二、直涂
直涂工艺,顾名思义,就是在质子交换膜上直接涂覆催化剂浆料,目前产能高的膜电极厂家都是采用双面卷对卷直涂工艺。个别厂家会采用一面热转印,一面直涂,避免直涂溶胀问题,同时提升效率。
阴极CCM涂布工艺
阳极CCM涂布工艺
卷对卷CCM涂布过程
生产步骤:
1. 制备催化剂浆料:
首先制备含有催化剂(如铂)、离子交换树脂、溶剂和其他添加剂的浆料。这种浆料必须具备良好的流变性质,以便于涂覆。
2. 选择质子交换膜:
选用适合的质子交换膜,要求能在燃料电池工作条件下提供良好的化学稳定性和电导率。
3. 涂覆过程:
使用直涂技术将催化剂浆料直接涂布在膜上。涂布方法可以是刷涂、喷涂、刮刀涂布或其他适合的涂覆技术。
涂布后,膜电极会在特定条件下进行干燥和热处理,以去除溶剂和确保催化剂层与膜的良好结合。
4. 干燥与热处理:
干燥过程中溶剂蒸发,留下固体催化剂和离子交换树脂。热处理则进一步改善催化剂层的结构,增强其与膜的结合力。
5. 压合过程:
处理后的膜电极与气体扩散层(GDL)一起压合,以形成完整的膜电极组件(MEA)。
优点与挑战:
优点:
- 成本效益:减少了催化剂的使用量,因为催化剂可以更精确地涂布在所需区域。
- 工艺简化:直接在膜上涂覆简化了制造过程,减少了组装复杂性。
- 性能提升:通过优化催化剂层厚度和均匀性,可以提高电池的性能。
挑战:
- 涂覆均匀性:需要高度控制涂覆过程,以确保催化剂层的均匀性和厚度一致。
- 干燥和热处理条件:必须精确控制,以防催化剂层损伤或与膜的结合不良。
- 溶胀问题:需要从设备、配方工艺方面来解决。
END
原文始发于微信公众号(艾邦氢科技网):膜电极催化剂层常见制备工艺:热转印、直涂
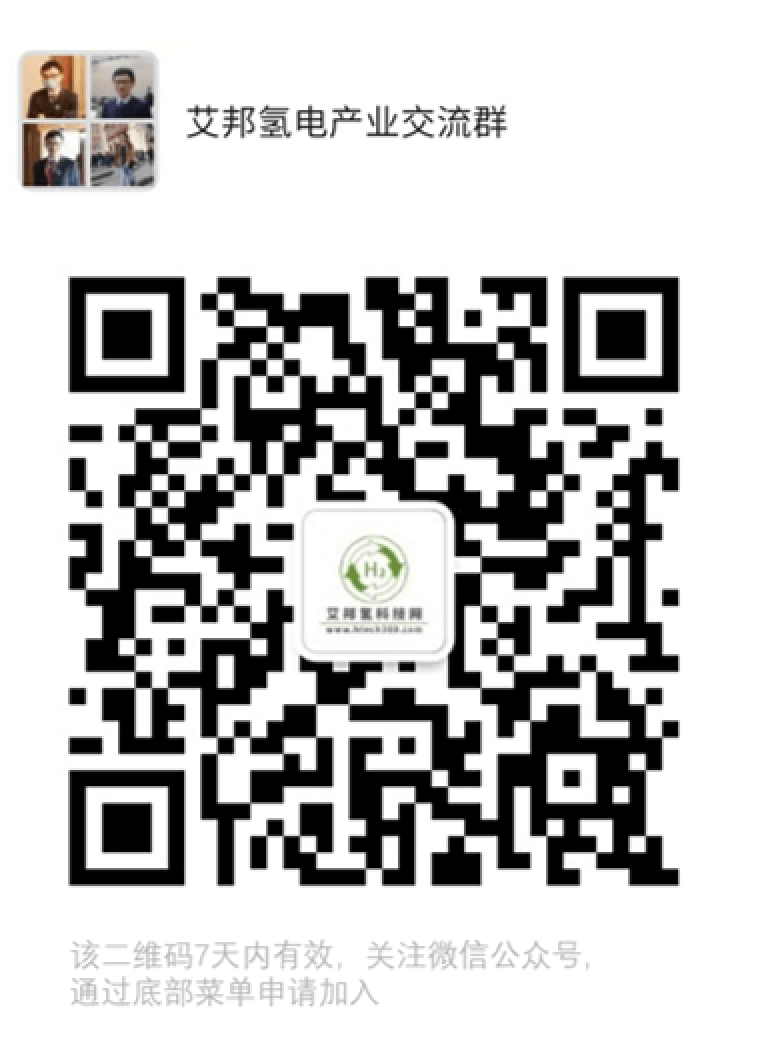