质子交换膜燃料电池堆是由一片片单电池串联组装而成的,其中,单电池由阳极板、MEA(膜电极)以及阴极板组成。通常,单电池的使用电压为0.6~0.85V,在集成燃料电池堆时可根据需要选择单电池的串联数量。
作为质子交换膜燃料电池堆的重要组件,双极板的质量占燃料电池堆的60~80%,成本占20~40%,并且几乎占据了整个燃料电池堆的全部体积。
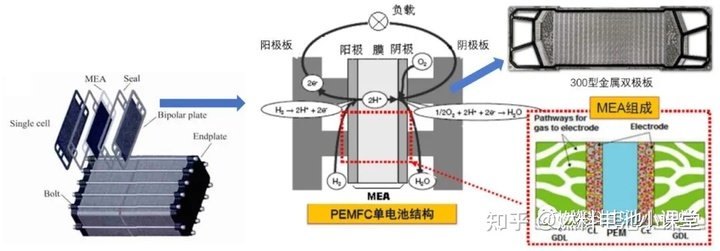
燃料电池电堆、单电池、双极板和MEA之间的关系示意图
在燃料电池堆内,双极板主要具有以下作用:
- 支撑MEA
- 分隔各单电池
- 分隔阴极、阳极反应气体,防止其相互混合
- 提供电气连接
- 输送反应气体并使之均匀分配
- 传导反应热量
- 去除水副产物
- 承受组装预紧力
根据材料不同,双极板可以分为石墨双极板、金属双极板以及复合材料双极板。以上三种材料的双极板各有优、劣势。前几年,石墨双极板是比较常用的双极板材料,但由于在批量生产时,金属双极板的生产成本相对较低,同时,大功率的金属双极板电堆比石墨双极板电堆在体积方面要小得多,因此,近年来金属双极板的应用越来越广。复合材料双极板由于生产周期长、成本高等缺点在应用方面受到很大限制。
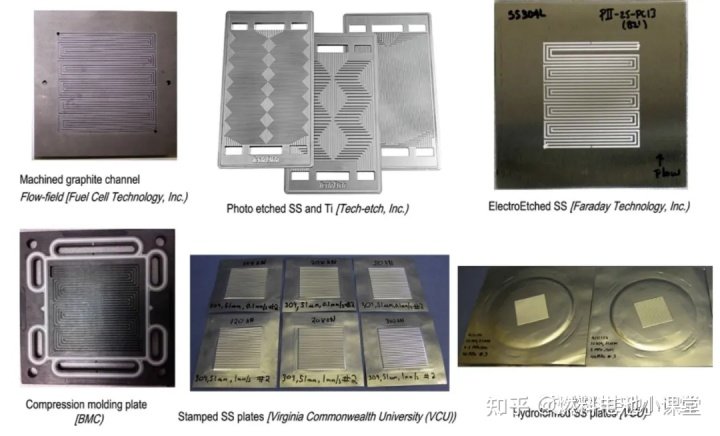
双极板图示
不同材料双极板的优缺点对比
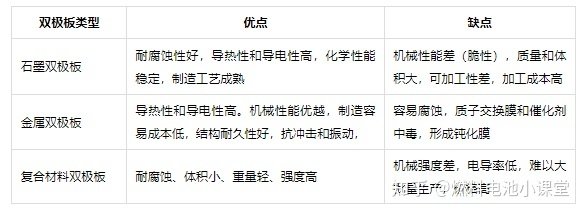
石墨双极板
石墨是热和电的良导体,具有较高的电导率、化学稳定性、热稳定性以及耐腐蚀、低密度等优点,用于制作双极板具有先天独特的优势。
由于石墨是一种多孔的脆性材料,强度低、延展性差(比较脆),难以满足双极板的气密性要求,因此在加工时,需要对石墨进行反复浸渍、碳化处理从而制造成无孔的具有良好气密性的无孔石墨双极板。
因此石墨双极板在加工制造时对制造工艺具有很高的要求,否则就容易使得制造成的双极板具有较高的孔隙,气密性较差,装成燃料电池堆不仅影响电堆的整体性能,还有可能导致氢泄露,造成安全隐患。
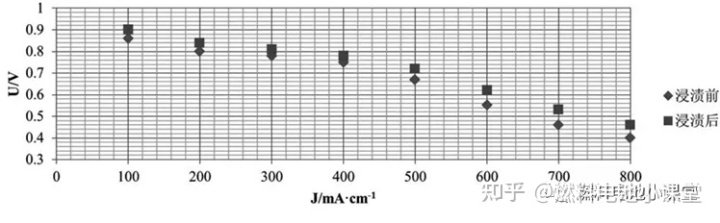
石墨双极板浸渍前后电池电堆性能对比
石墨双极板的生产制造方式主要有三种,即机加工、注塑和模压,根据不同的工艺需求石墨可以制作为粉末、卷材、板材和乳液,但其原材料主要分为以下三类:
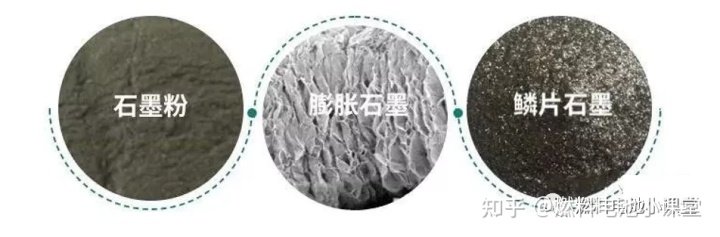
石墨粉:化学反应很灵敏的物质,在不同的环境里面他的电阻率都会变,取决于石墨粉在绝缘的物体里面是否能够保证石墨粉不间断。耐高温性、化学稳定性、可塑性和抗热塑性都很好。
膨胀石墨:由天然石墨鳞片经插层、水洗、干燥、高温膨化得到的一种疏松多孔的蠕虫状物质。除了具备天然石墨本身优良性能以外,还具有天然石墨所没有的柔软、压缩回弹性、吸附性、耐辐射性等特性,膨胀石墨遇高温可瞬间体积膨胀150~300倍。
鳞片石墨:结晶完整,为天然显晶质石墨,其形似鱼磷状,属六方晶系,呈层状结构,片薄且韧性好,物化性能优异,具有良好的热传导性、导电性、抗热震性,耐腐蚀性等。
下面分别详细介绍每种加工方式的工艺流程。
1.1 石墨双极板的制造方式--机械加工
石墨双极板的机械加工工艺流程如下:
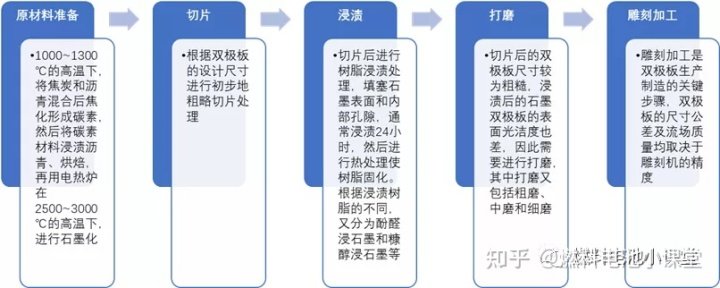
石墨双极板机械加工工艺图示
机械加工的局限性:
1.前面提到石墨是一种强度低、脆性强的材料,因此机型加工难以适用于超薄双极板的制作(<1.5mm);
2.机械加工过程中可能会导致刀具与石墨的摩擦过大,导致双极板的尺寸精度和表面质量较差。
目前,国内生产石墨双极板的厂家大多采用机械加工的方式,这种方式虽然节省了开模费用,但是制作工艺复杂,加工周期长,成本高。
1.2 石墨双极板的制造方式--注塑成型
注塑成型是将一定比例的石墨和树脂混合料从注塑机的料斗送入机筒内,被加热融化后的混合料通过加压经由喷嘴注入闭合模具内,经冷却定型后脱模得到成品。
为了提双极板的导电性,可以在混合物中加入一定量的金属粉末,除此之外,还可以加入碳纤维或陶瓷来提高机械强度。
注塑成型的局限性:
1. 长时间的粘结剂去除,厚界面开裂,尺寸限制等;
2.进一步石墨化虽然能够提高双极板的性能,但同时也使得成本大增,因此,目前注塑成型不适合用于大规模生产。
1.3 石墨双极板的制造方式--模压成型
石墨双极板的模压成型工艺流程如下:
1. 制备石墨粉与树脂的混合材料
2. 混合材料和模具进行前处理
3. 采用聚合物的熔融温度和一定压力,使得粉末在模具中流动并充满整个型腔,固化脱模后得到双极板。
注:粘结剂如为热固性塑料,通常只需几分钟就能固化脱模,粘结剂如为热塑性塑料,则需将模具冷却到粘结剂熔点以下的温度后脱模。
石墨双极板模压成型在批量生产方面具有较强的优势,但是,由于目前燃料电池整体需求量相对不大,同时,双极板的外观尺寸多样,并没有严格的国标要求双极板的外观一致性,如采用模压成型,就使得双极板厂家针对不同的设计尺寸分别开模,在出货量不足的前提下,开模能本难以均摊。因此,在目前示范运营阶段,再加上自家产品前景不明的情况下,多数双极板厂家都不乐意为模压成型过早投入较高的成本
石墨双极板总结
由于石墨是热和电的良导体,具有较高的电导率、化学稳定性、热稳定性以及耐腐蚀、低密度等优点,用于制作双极板具有先天独特的优势。同时在耐久性方面,石墨双极板有先天优势。但同时由于批量化生产问题,以及在超薄方面实现起来比较有难度,因此相较于金属双极板,石墨双极板的劣势也同样明显。
金属双极板
与石墨双极板相比,金属双极板具有与之类似的高导电、导热能力,但金属双极板具有更好的机械强度、阻气能力和抗冲击能力,因此,金属双极板能够做到超薄,大幅提升比功率密度。
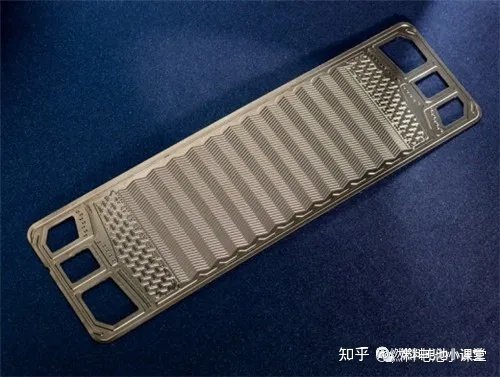
金属双极板图示
同时,金属双极板机械加工性强、制作工序较少、可制作超薄双极板甚至可小于1mm,并且量产工艺成熟,大幅降低的热容使金属板具备了更强的低温启动能力,并且可以大幅降低量产成本,因此,金属双极板备受行业内关注。
目前,主流的冲压双极板制造方案Borit公司生产双极板的流程类似。除了最初的双极板设计(包括外观、轮廓、厚度、流道等),金属双极板生产流程中主要包括以下六步:
1. 材料准备
制造燃料电池金属双极板时,带材的选择一般有两种,一种是预先做过涂层处理的带材,一种是未经涂层处理的带材。
经涂层处理的带材,如SANDVIK提供的预涂层处理钢带产品,采用先进的环保真空镀膜工艺制得,主要特点有:
- 钢带和涂层之间具有优异的附着力
- 导电性极佳
- 高耐腐蚀性
- 带材厚度0.05~0.8mm
下图为SANDVIK涂层钢带的制造过程:①为清洁/检查;②为上涂层(采用连续蒸发工艺);③为检查(采用X射线检测设备用于测量涂层的厚度和质量);④为测试、分切和包装。
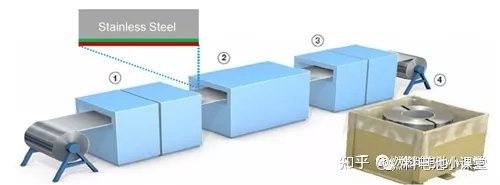
SANDVIK涂层钢带制作过程
SANDVIK SANERGY®LT预涂钢带可用做PEMFC双极板,并能进行大规模生产且生产成本低。
其主要特点有:具有良好的界面接触电阻,与金或石墨相当(根据DoE(美国能源部)要求(<10mΩcm -2));PEMFC环境中的腐蚀<1μA/cm2;采用气密材料;电气降解率低(低于0.5%/ 1000小时);良好成型性/涂层附着力。
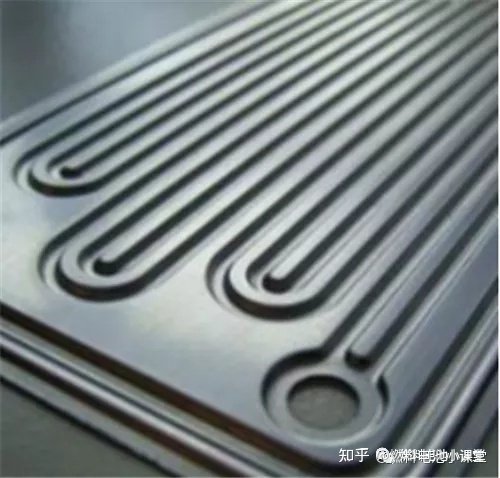
SANDVIK SANERGY®LT预涂钢带用于PEMFC的双极板
使用预涂层处理钢带,通常不需要在极板成型后进行涂层处理,可以更快更便宜地生产双极板,但其涂层稳定性经过加工和焊接处理后容易出现问题。
目前市面上除了丰田,金属双极板在生产过程中使用未经涂层处理的不锈钢带材居多。以Interplex公司的双极板制造为例,其使用的带材材料为SU316L不锈钢,厚度大概在 0.075 – 0.1mm。
2. 成型和分割
带材清理后,便会进行成型和分割,生产出阴极板和阳极板。各双极板厂商的成型方式和流程可能会有所不同,如下图使用的是冲压成型方式。
2.1 冲压成型
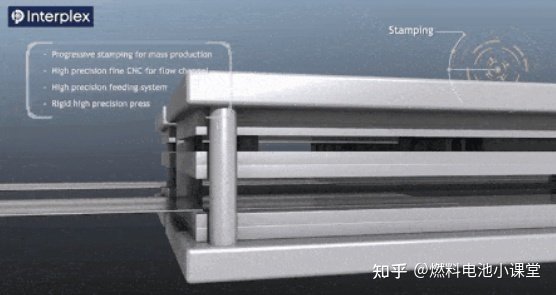
冲压成型工艺图示
冲压工艺是用压力装置和刚性模具对板材施加一定的外力,使其产生塑性变形,从而获得所需形状或尺寸的一种方法。
冲压坯主要为热轧和冷镦钢板,占世界钢材的 60%~70%。因此,从原材料的角度来看,冲压工艺占主导地位。而且,冲压工艺生产的双极板成本低和生产率高,具有薄(低至 0.051 mm)、均匀和高强度的特性,广泛用于汽车,航空航天和其他领域。
2.2 液压成型
有些厂家液压成型方式,如下图所示
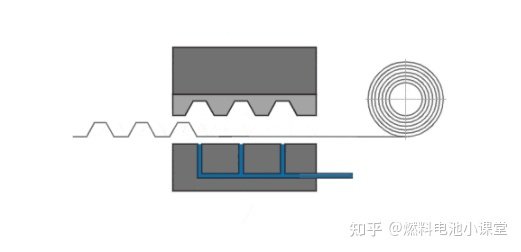
液压成型工艺图示
液压成型工艺是一种利用液体或模具作为传力介质加工成产品的一种塑性加工技术,液压成型原理图下图所示。
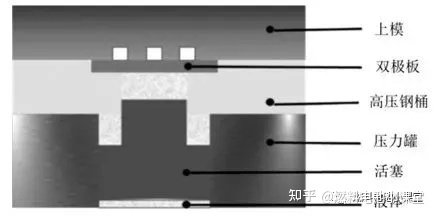
液压成型原理图
与冲压工艺相比,液压成型的模具需求量少(只需要一套模具)。液压成型在尺寸和表面质量方面优于冲压工艺,而冲压工艺具有较高的生产率。
2.3 橡胶垫成型
部分厂家也会使用一些其他的成型方式,如橡胶垫成型工艺。橡胶垫成型工艺,也称为柔性成型工艺,是一种用于微/中型流道成型的新型冲压方法,该方法可以解决冲压和液压成型过程中可能出现的裂纹、皱纹和表面波纹等问题。
橡胶垫成型原理下图所示,由一个刚性模具和一个橡胶垫组成,它们之间为柔性接触,极大提高了微尺度流道的可成型性。
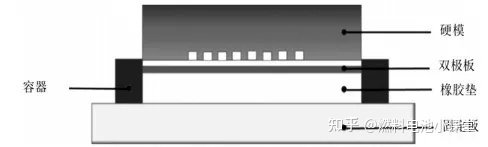
橡胶垫成型工艺原理图
橡胶垫成型工艺的优势在于,橡胶垫和刚性模具不需要在成型过程中精确组装,从而可以大大减少时间和成本。这种成型的主要缺点是橡胶垫的使用寿命短,需要经常更换。
2.4 蚀刻
另外,有些厂商在小批量生产时也常常采用机加工方式或蚀刻的方式使双极板成型,机加工的方式大家应该都能想象得到,这里就不再多加叙述了。这里,刻蚀给大家展开说一下。
蚀刻是将材料使用化学反应或物理撞击作用而移除的技术。蚀刻技术可以分为湿蚀刻)和干蚀刻两类。
蚀刻最早可用来制造铜版、锌版等印刷凹凸版,也广泛地被使用于减轻重量(Weight Reduction)仪器镶板,铭牌及传统加工法难以加工之薄形工件等的加工;经过不断改良和工艺设备发展,亦可以用于航空、机械、化学工业中电子薄片零件精密蚀刻产品的加工,特别在半导体制程上,蚀刻更是不可或缺的技术。
所以说,蚀刻并不是什么新兴的加工技术,只是随着不断改良和工艺设备发展,也被应用于高精密设备。其中较为广泛地被使用于类似于线路板线路蚀刻制作以及铭牌及传统加工法难以加工之薄形工件等的加工,因此蚀刻工艺对于制造薄型金属极板来说,是一种合适的工艺路径。
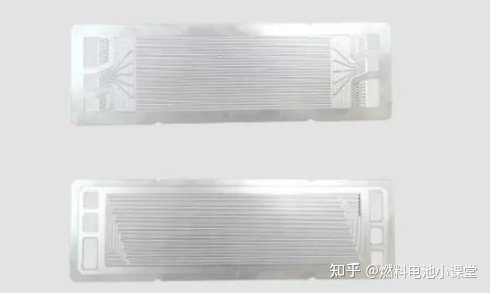
蚀刻出的双极板图示
3 质量检测
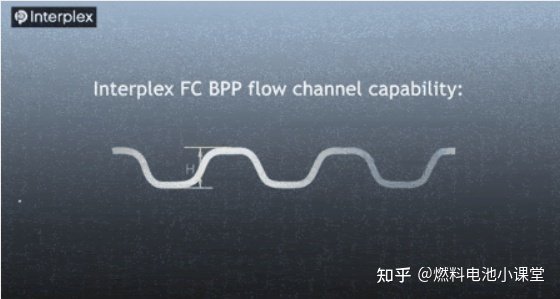
单片的极板制造完成后,需对每片极板进行质量检测,判断脊和沟的尺寸、厚度和误差等各项数据是否满足设计要求。
4 激光焊接
满足质量要求的阴、阳极板通过激光焊接焊接固定在一起,构成一个完整的双极板,经过焊接后,焊缝会将双极板的冷却剂腔体完全密封。
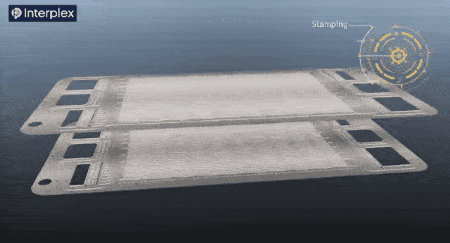
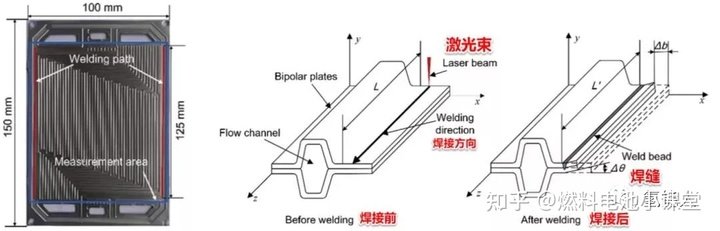
双极板的激光焊接方式如上图所示。激光束沿着双极板周边设计好的密封槽进行焊接,激光行经之处,所产生的的焊缝如下图所示,将阴阳极板连接起来。
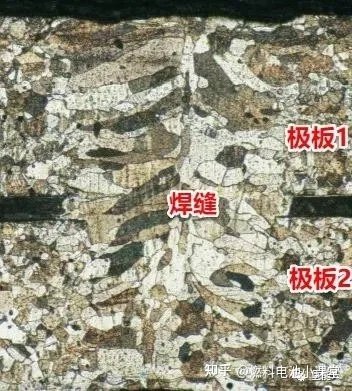
焊接后,会将双极板的冷却剂腔完全密封,最后还会对其进行密封性能检测。
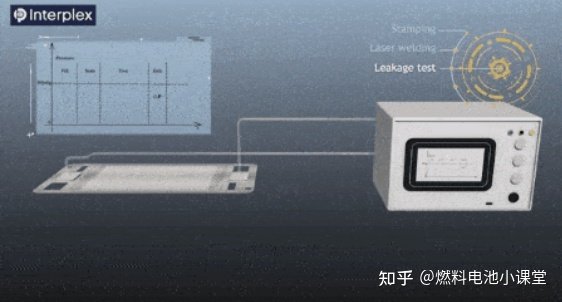
5 涂层处理
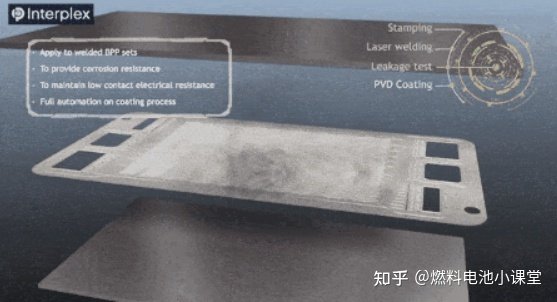
双极板焊接完成后会被进行涂层处理,来提高双极板的耐腐蚀性能。目前,常用的涂层处理方式为使用PVD方法。
6 密封
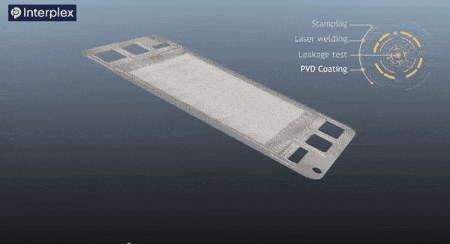
最后,在双极板上设计好的密封槽内填入密封材料。这一步不同厂家的设计都会有所不同,有的厂家使用定制的密封圈圈贴上双极板,如下图所示。
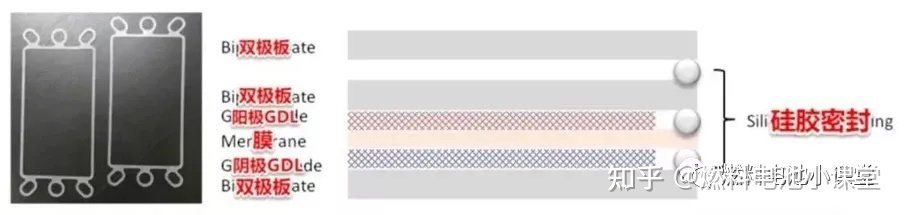
密封圈密封图示
有的厂家通过点胶密封,还有的厂家使用与GDL集成在一起的密封圈,如下图所示。
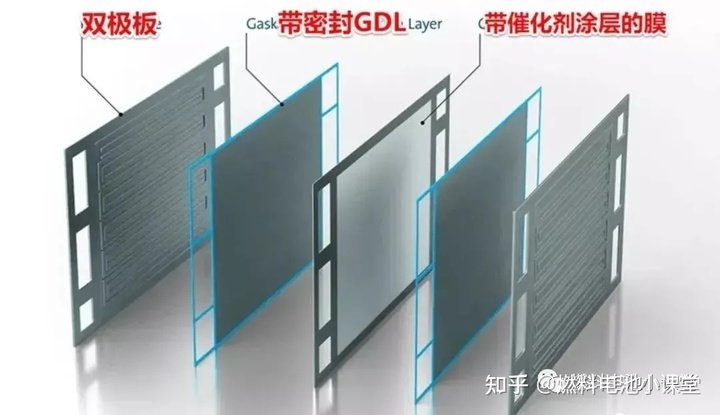
因此,双极板厂商的生产流程中不一定包含这一步。
复合材料双极板
复合材料双极板由两种或两种以上的材料组成,通过复合其他材料优化了其机械性能,克服了石墨材料及金属材料的缺陷,且兼具石墨材料的耐腐蚀性和金属材料的高强度特性。
复合双极板按照结构可分为结构复合双极板和材料复合双极板。
3.1 结构复合双极板
结构复合双极板是以薄金属或其它高强度、高致密性的导电板作为分隔板,以有孔薄碳板、金属网等作为流场板,以导电胶黏合。这种复合结构双极板结合了金属板与石墨板的优点,由于金属板的引入,使石墨只起导电与形成流道的作用,而不需要致密与增强作用,同时由于石墨板的间隔,金属板不需要直接接触腐蚀介质,减轻了金属双极板的腐蚀,这样使得双极板具有耐腐蚀、良导电、体积小、质量轻、强度高的优势,但缺点是制作过程较为繁琐,密封性相对较差。
3.2 材料复合双极板
材料复合双极板主要是通过热塑或热固性树脂料混合石墨粉/增强纤维形成预制料,并固化/石墨化后成型。复合材料型双极板又可以分为碳基复合材料双极板和金属基复合材料双极板。下表列出了金属基和碳基材料复合双极板的研究情况。
金属基和碳基复合材料的研究情况
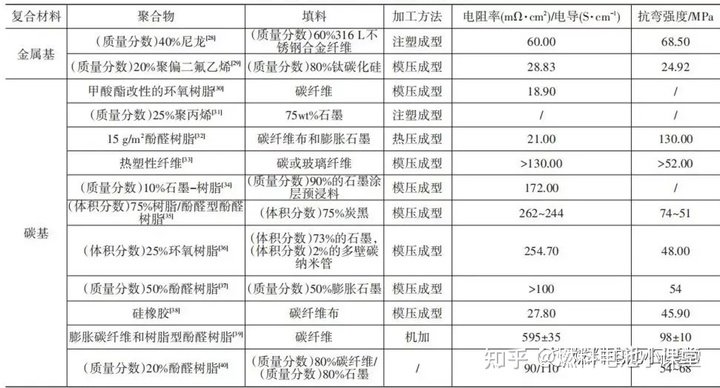
碳基复合材料双极板可以根据导电填料及树脂配比调整双极板的导电性能和机械强度,可以采用模压或注射成型工艺进行批量化生产,降低双极板制造成本,未来具有较大应用前景。金属基复合材料双极板通常采用金属作为分隔板,边框采用塑料、聚矾、碳酸酯减轻电池组的质量,边框与金属板之间采用导电胶粘接,以注塑与焙烧法制备的有孔薄碳板或者石墨板作为流场板。
金属基复合材料双极板集合了石墨双极板和金属双极板的优点,但是由于其结构及制备工艺复杂,难以实现批量化生产,生产成本远高于碳基复合材料双极板,在 PEMFC中推广有一定困难,但是对于特殊场景用途具有一定优势。
更多燃料电池技术信息请关注公众号“燃料电池小课堂”!
原文始发于:燃料电池双极板技术详解
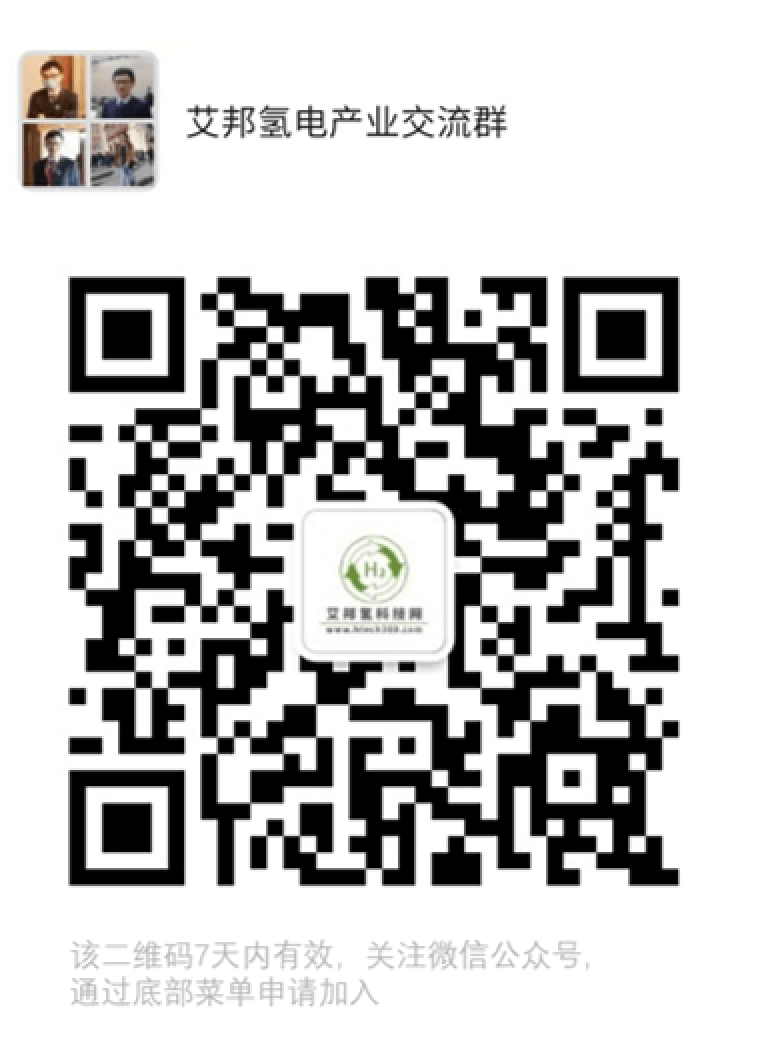