文/潘金龙,胡佳伟,谢卓华·珠海格力电器股份有限公司
板材模内液压成形技术是指利用液体介质代替凸模或凹模,靠液体介质的压力使板材成形的一种加工工艺。在成形过程中,凹模上表面与坯料下表面有液体溢流,产生溢流润滑的作用,减少凹模与板料的摩擦力提高材料变形均匀性,从而提高板材的成形极限。板材模内液压成形技术用液体介质代替凹模或者凸模,可以减少一部分模具材料、模具加工费用,并且降低模具的整体装配精度要求,缩短模具制造周期。此工艺可以成形形状复杂、成形后的零件精度要求高、表面质量要求高的零件,零件制造成本也较普通冲压工艺低30%以上。
板材模内成形技术从最初的橡皮膜液压成形技术开始,然后出现了充液拉深技术、充液变薄拉深技术、无模充液拉深技术等。随着汽车制造业飞速发展,汽车蒙皮件的形状日趋复杂。以及铝、镁等质量较轻,但成形性能较差的新材料的不断投入使用,使得人们开始将板材模内液压成形技术作为研究重点并将其广泛应用。尤其在目前全球重点发展的新能源燃料电池领域,板材模内液压成形技术对双极板的成形质量方面将会有较大提升作用,大大改善双极板的开裂和回弹问题。
本文对一款燃料电池双极板的成形工艺进行了研究,对其主要成形工艺参数进行了理论计算,并根据回弹分析及试验,优化了产品结构及成形工艺参数。
模内液压成形工艺过程
板材模内液压成形工艺过程可以分为四个阶段,如图1所示。
图1板材模内液压成形工艺过程
⑴充液阶段:开动水泵或油泵将液体介质充满凹模型腔至凹模表面。
⑵施加压边力:将板材毛坯料放在凹模表面上,利用弹簧或氮气弹簧施加压边力FQ。
⑶成形阶段:凸模在油压机的压力下开始压入凹模,通过自然增压或者液压系统使凹模内的液体介质建立起压力Pcr,将板材毛坯料渐渐压贴在凸模上,直至成形结束。
⑷板材模内液压成形有如下优点:
①材料成形极限高;
②成形零件表面质量好,无擦痕、压印等缺陷;
③成形回弹小,尺寸精度高;
④可以成形复杂零件和铝、镁等质量较轻、性能较差的零件;
⑤成形变薄均匀,开裂风险低。
回弹分析
本文研究的燃料电池双极板,材质为不锈钢316L,厚度0.1mm,硬度160~170HV,如图2示。
图2 产品图
该型面有小圆角R0.15,成形有一定难度。型面有一定曲率,成形后回弹较大,需要保证一定的减薄量,从而增加塑性应变,减少弹性应变,来减小回弹。所以,压型设计了工艺辅助面和阻延筋,以增大塑性应变,减少弹性变形,如图3所示。同时,利用回弹补偿,最终得以有效控制成形零件的回弹。
利用CAE分析软件,对该零件成形回弹数值进行仿真模拟。在分析中采用欧标材料特性14404,根据单向拉伸试验数据设置材料参数。坯料网格划BM-5单元,模具网格、法线夹角采用三角形单元。在分析中,坯料与凹模、坯料与压边圈坯料与凸模的摩擦因数设为0. 15。
对未进行任何处理的原零件模型和设计了工艺辅助面、阻延筋的零件模型分别进行仿真分析,分析结果如图4、图5所示。结果显示,设计了工艺辅助面和阻延筋的零件在零件中部区域回弹量明显优于原零件。最终选用设计了工艺辅助面和阻延筋的零件进行生产。
(II为工艺辅助面剖视图,III为阻料筋剖视图)
图3 成形工艺图
图4 原零件回弹分析结果
图5 设计了工艺辅助面和阻延筋的零件回弹分析结果
模具设计
双极板模具结构如图6所示。模具由上模和下模组成,上模包括凸模、压料板、氮气弹簧等,下模包括凹模板、密封圈、压力传感器等。凸模是成形关键零件,决定产品形状和尺寸,氮气弹簧提供初始压边力;压料板在氮气弹簧的作用下压住产品,控制材料流动;凹模板的液室储存液体介质,并连接外部高压液体介质;压力传感器检测液室压强;密封圈起密封作用,防止液体介质泄露。
此结构通过压力传感器实时监控液室压强,压力传感器与冲压设备、增压设备控制电路连接,并将液室压强信号传递给冲压设备和增压设备。当液室压强超过上限值则冲压设备立即停机,防止液室压强过大损坏模具;当液室压强小于下限值时将压强信号传递给增压设备调整压强,防止因液室压强不足而造成产品尺寸不合格。
图6 双极板模具结构图
试验分析
为了选取最合适的液室压强,对不同液室压强下制造产品流道深度与流道内R角进行测试。取出产品测量流道深度H和流道内R角。试验测试结果如图7、图8所示。
图7 流道深度随压强变化图
图8 流道内R角随压强变化图
通过图7与图8可以得出,双极板流道深度随着液室压强增大而增大,当液室压强达到90MPa时,深度达到图纸要求尺寸0.4mm;双极板内R角随着液室压强增大而减少,当液室压强达到95MPa时达到图纸要求尺寸R0.15mm。综合以上结论,选取95MPa作为液室压强。
结束语
通过计算、仿真分析及实验验证,得出以下结论。
⑴板材模内液压成形工艺可以提高材料拉伸极限,减少开裂风险。另外,该工艺可以使材料流动更加均匀,内应力更加一致,可有效降低回弹。
⑵对于尺寸精度要求高的产品,为了进一步减小回弹,提高产品尺寸精度,可以通过增加塑性应变,减少弹性应变的措施来实现,如液压成形工序设计控制材料流动的工艺面和阻延筋等。
⑶液压成形模具压边力采用氮气弹簧提供,不宜使用普通弹簧,因为普通弹力初始压力小,不能有效密封,容易发生泄漏。
⑷产品型面深度随着液室压强增大而增大,型面R角随着压强增大而减小,深度先于R角成形到位;成形所需压强取决于产品材质、产品厚度、产品最小R角、模具压边力等。
作者简介
潘金龙,样品室主任,模具工程师,主要研究方向:模具、增材制造技术;2021年主导完成超薄金属板冲压及焊接成形关键技术研究项目获得珠海格力电器股份有限公司科技进步奖七等奖,拥有6项专利技术。
——文章选自《锻造与冲压》2022年第20期
原文始发于微信公众号(锻造与冲压):燃料电池双极板模内液压成形的数值模拟与试验
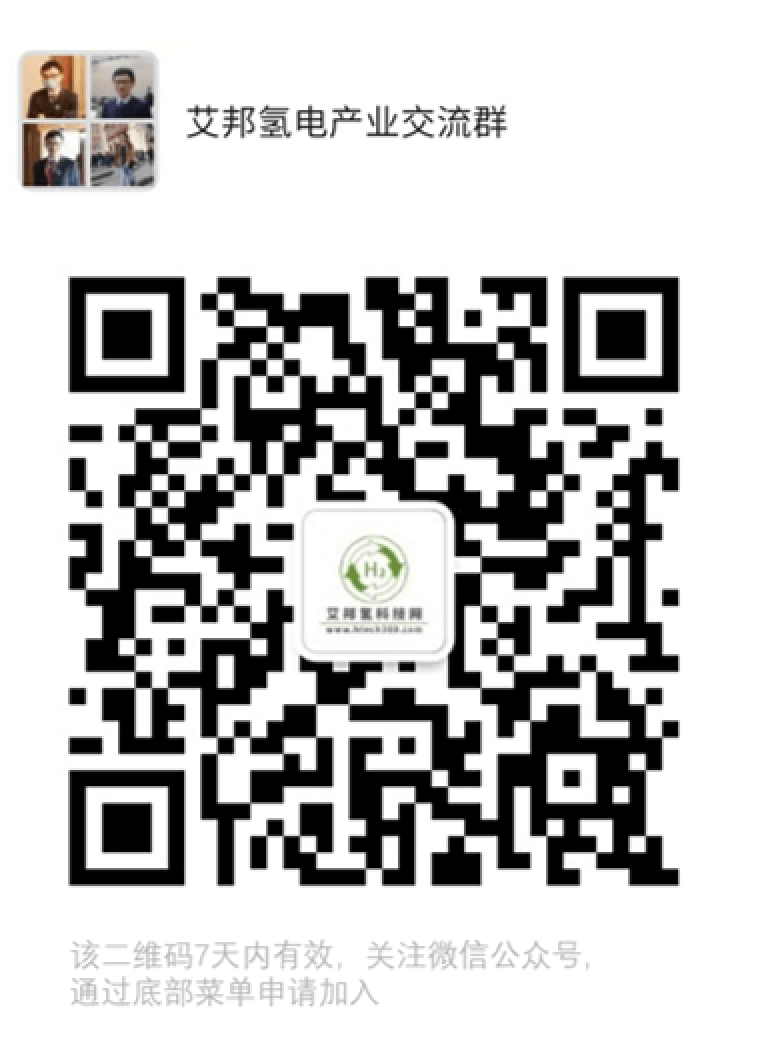