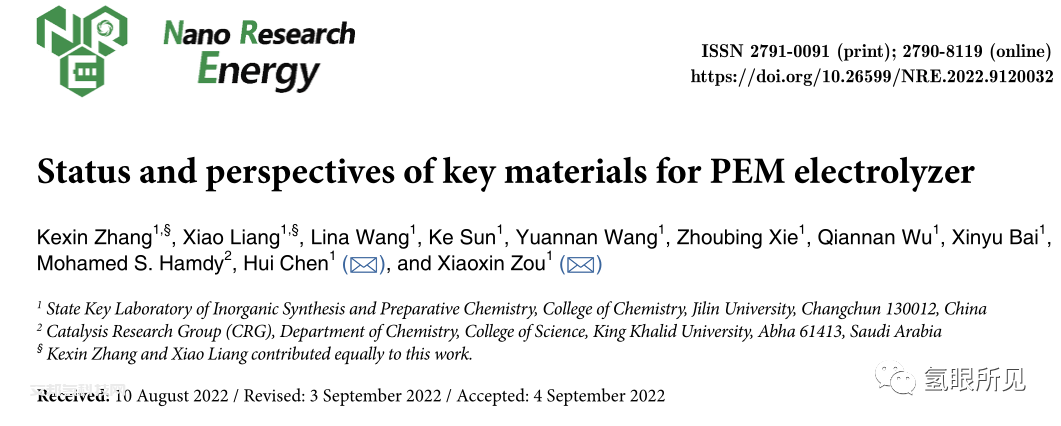
一、堆的结构
在PEM电解槽中,核心部件主要包括BP(流场板)、GDL(气体扩散层)、PEM(质子交换膜)、阴极和阳极电催化剂。下图1(a)显示了PEMWE堆栈中单个单元的示意图。两个半电池被PEM隔开,PEM在反应过程中运输质子,并阻止产物气体的通过。催化剂直接涂覆于膜或多孔传输层上。在大多数电池设计中,催化剂层沉积在膜上,形成电池的关键成分,即MEA(膜电极)。两个多孔传输层(也称为GDL)夹在MEA的两侧。流场板(也称为BP)封装了两个半电池,作为电荷、质量、热量的传递,并与外部电源建立联系。氢和氧产物通过催化剂表面,GDL和BP依次释放出电池。准确地说,半电池还需要补充一些密封元件,以防止气体和水的泄漏。
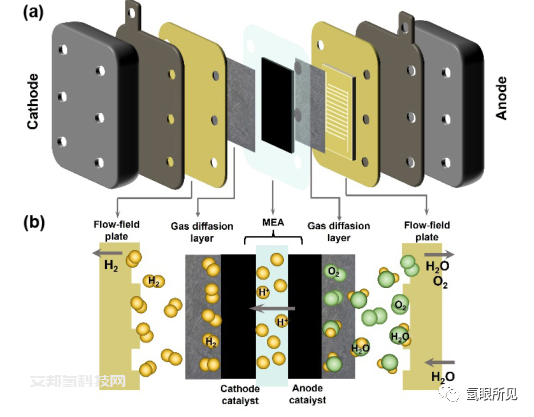
图1:PEMWE的堆栈结构和关键材料
上述核心部件对PEM水电解制氢的成本、性能和使用寿命具有重要的影响。BP和GDL在堆栈成本中所占比例最大,分别为51%和17%。氧化和腐蚀的操作环境限制了材料主要是使用高级钛基材料,还需要诸如Pt和Au等做保护涂层。为了降低整个电解槽的成本,开发廉价的替代材料是必要的。相对而言,PEM和催化剂在PEMWE电解槽中所占比例较小,分别为5%和8%。另外,MEA的制造过程需要占用整个电解槽成本的约10%。显然,实现高效的水电解性能,同时将材料成本降到最低,仍然是PEMWE面临的巨大挑战。
MEA是PEMWE的核心,由PEM、阴极和阳极电催化剂组成,也在很大程度上决定了水电解的性能。理想的PEM应能满足多种功能要求,包括低透气性、优异的质子导电性、良好的吸水性、低溶胀比、优异的化学和机械稳定性、低成本和高耐久性。到目前为止,全氟磺酸(PFSA)膜是PEMWE常用的商用PEM。该膜具有疏水的铁氟龙样骨架和亲水的磺酸侧链。根据等效重量(EW)、侧链化学结构和长度,PFSA可以分为不同的膜(下图2),如Nafion、Aciplex、Flemion、3M和短侧链(SSC)等。其中,杜邦公司生产的Nafion系列膜是具有代表性的一类。Nafion 117、115和112是该系列中使用最多的膜,不同的数字代表不同的等效重量和厚度,对电解槽的整体性能有显著影响。膜的厚度会影响PEMWE的离子电导率,实验证实膜越薄,欧姆电阻越小,电解槽性能越好。
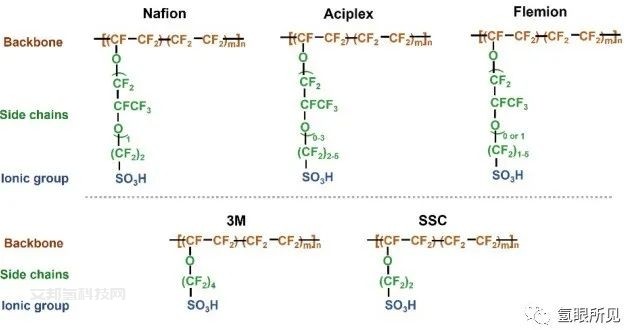
图2:各种PFSA聚合物电解质膜的化学结构。
然而,使用过薄的膜可能会给PEMWE带来一些问题,例如增加气体渗透性降低氢纯度,降低机械强度和耐久性,以及潜在的安全隐患。值得注意的是,PEMWE中的气体交叉是致命的。一旦气体穿透,氢气与氧气反应释放出大量热量,这将破坏薄膜和整个电堆。针对这些问题,有研究提出,通过在有催化剂支撑的两层膜之间使用含有Pt纳米颗粒的中间层,从阴极侧向阳极侧渗透的氢气可以与氧气重新结合,可以显著降低氢气的渗透。此外,Nafion—石墨烯—Nafion的PEM夹层结构由Bukola及其同事设计。石墨烯的特殊性质可以允许质子通过,但阻碍了氢的传输,这使得夹层结构表现出高质子传导性和低八倍的氢交叉。
虽然nafion膜已经成熟为商业化应用的膜,但其缺点是成本高,且在高温条件下(> 100℃)质子导电性降低。高温水电解可降低吉布斯自由能变化,改善电极动力学,但PFSA膜在此条件下会发生降解。因此,Nafion基复合膜和碳氢化合物膜受到了研究者的广泛关注。Baglio等和Antonucci等人制备了Nafion-TiO2膜和Nafion-SiO2膜,并证明其工作温度可以在100℃以上。这些无机金属氧化物填料是吸湿的,使复合膜有更好的保水性和更均匀的水分布,从而降低欧姆电阻,反过来显示更好的电池性能。碳氢化合物膜在20世纪80年代初首次被开发出来。在高温操作的驱动下,磷酸(PA)掺杂的聚苯并咪唑(PBI)由于其高的无水质子导电性和低的蒸气压,被发现可以在100℃以上的温度下工作,被研究者广泛研究。然而,该膜不能达到长期耐用性,这可能是由于氧化条件下磷酸(PA)的化学侵蚀。综上所述,PEMWE的发展离不开质子交换膜技术的进步。如何加强膜的机械和化学稳定性,降低成本是膜的发展方向。值得注意的是,由膜引起的安全问题也应予以考虑。
膜电极的制备也是建造电解槽的重要组成部分。目前,MEA主要有两种构型(见下图3),即催化剂包覆膜构型(CCM)和多孔传输电极构型(PTE)。PTE结构是催化剂直接沉积在多孔传输层上。在这种情况下,PTE的孔径需要优化,因为小的孔隙会产生过大的传质阻力,而大的孔隙会导致催化剂渗透到PTE中,导致催化剂利用率低。然而,也有研究表明,在750mA/cm2以上的高电流密度下,PTE结构具有更好的极化行为,因此表现出比CCM结构更好的性能。在膜与催化剂之间的接触过程中,膜与催化剂之间的接触可以降低界面阻抗,提高质子的导电性和耐用性。但是,这种模式可能会引起膜的溶胀,因此需要更加小心地处理。此外,Holzapfel等人提出了一种新的膜电极制备方法,即直接膜沉积(DMD)。DMD - MEA(下图3)最右侧的图示是通过将膜直接沉积在阴极电极上制备的,其欧姆和传质损失减小,从而具有更好的电化学性能。值得注意的是,低催化剂负载DMD - MEA的气体交叉和性能分析将是未来研究的关键问题。该方法为MEA的制备提供了一种新的思路。
图3:PEMWE中三种MEA配置示意图
CCM是通过转印或直接在膜上涂布的方法制成。直涂方式技术上比较简单(但有溶胀和变形问题),但是转印能够避免膜的溶胀和变形。MEA的涂布方法一般包括喷涂(超声波或气溶胶)、卷对卷(如槽模、凹版和刀)和手工涂布等将催化剂涂在膜上。超声波喷涂法(下图4)适用于实验室小规模制备CCM膜,可精确控制催化剂涂覆量,且可靠、可重复性。
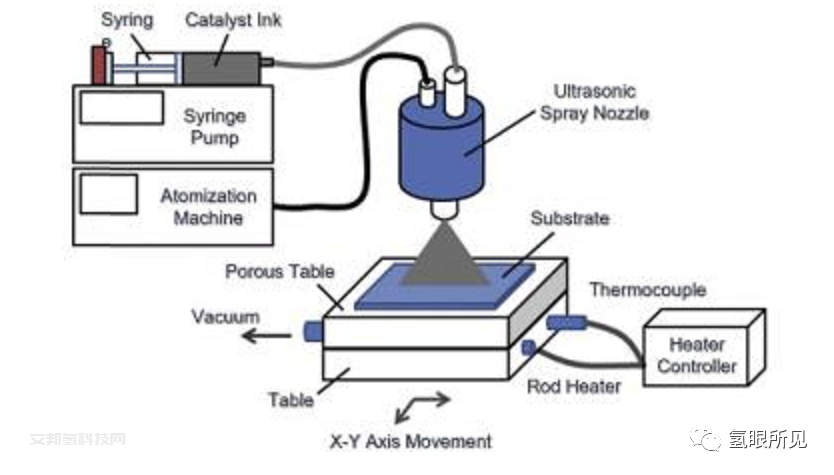
图4:超声波喷涂法
槽模涂布、凹版涂布、刮刀涂布等卷对卷涂布方式(下图5)可实现连续涂布,提高了生产效率,降低了成本。这种涂覆方法需要对浆液成分(如溶剂和固体含量)和加工条件(如干燥温度)进行优化,以达到与实验室规模的催化剂电极相比有更好的性能。
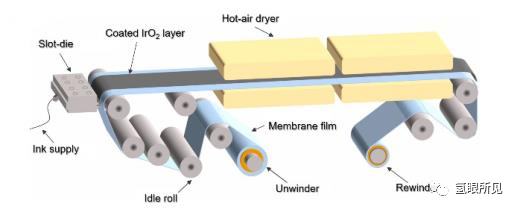
图5:卷对卷连续涂布法
随着PEMWE应用的扩大,利用卷对卷涂覆技术实现膜电极的大规模生产将是未来的趋势。值得一提的是,3M开发了纳米结构薄膜(NSTF)电极,其阴极和阳极分别使用Ir和Pt催化剂。NSTF催化剂的制备方法是在一种特殊的临时衬底微结构催化剂转移衬底(MCTS)上生长二甲苯红晶须,然后将催化剂以棒状阵列结构(下图6)沉积在其上。这样的制备过程可以使催化剂均匀沉积,并且可以以卷对卷的方式批量生产NSTF催化剂。
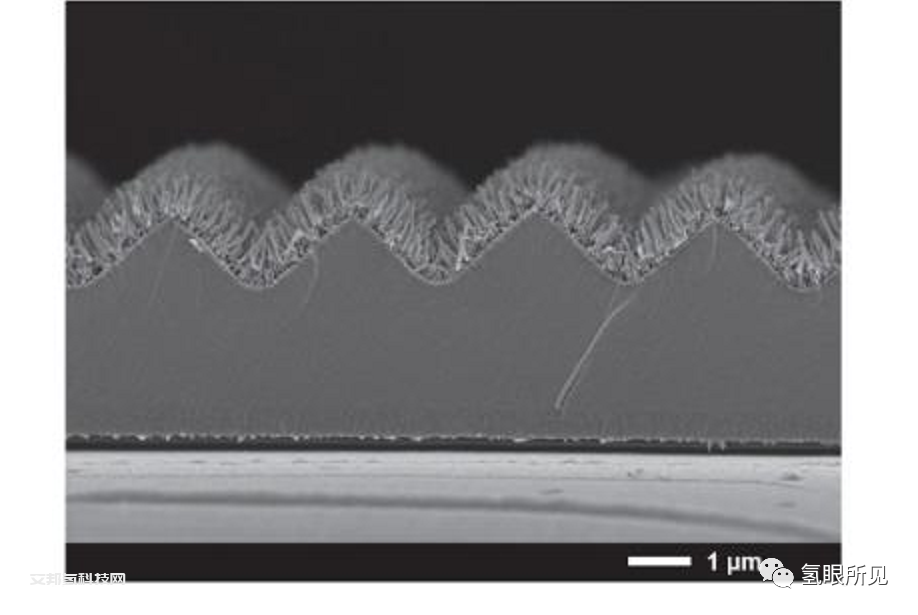
图6:在MCTS薄膜上生长的NSTF催化剂的横截面图像放大。
下图7显示了NSTF催化剂在三个代表性阶段的性能改善情况。由于NSTF催化剂的结构催化活性的提高以及催化剂与膜之间导电性的提高,使其性能得到了极大的提高。目前,NSTF催化剂在燃料电池中得到了很好的发展,相信它在电解槽中的商业化只是一个时间问题。
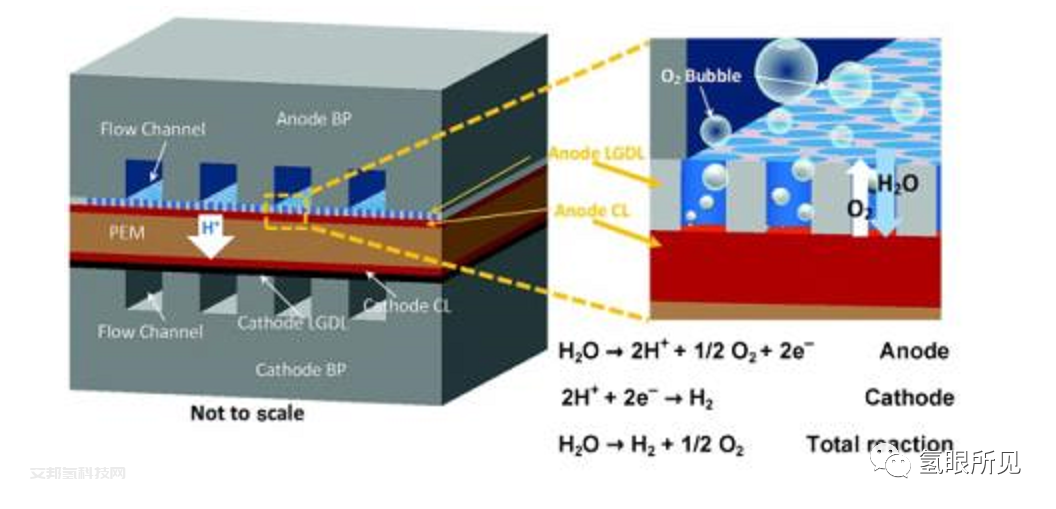
图7:2009 - 2014年3M NSTF催化剂研究进展
三、气体扩散层(GDL)
GDL是质子交换膜和BP之间的多孔介质(下图8)。液/气两相流体通过GDL通道被输送到催化剂层,在那里水在催化剂阳极分解为电子、O2和质子。氧气通过催化剂层和GDL回流到分离板,然后离开电池。电子通过GDL、BP和外部电路到达阴极侧。同时,质子通过PEM到达阴极,在那里它们与电子反应生成氢。然后H2流经阴极GDL并离开电池。只要维持水流和电解条件,H2/O2就会持续生产。
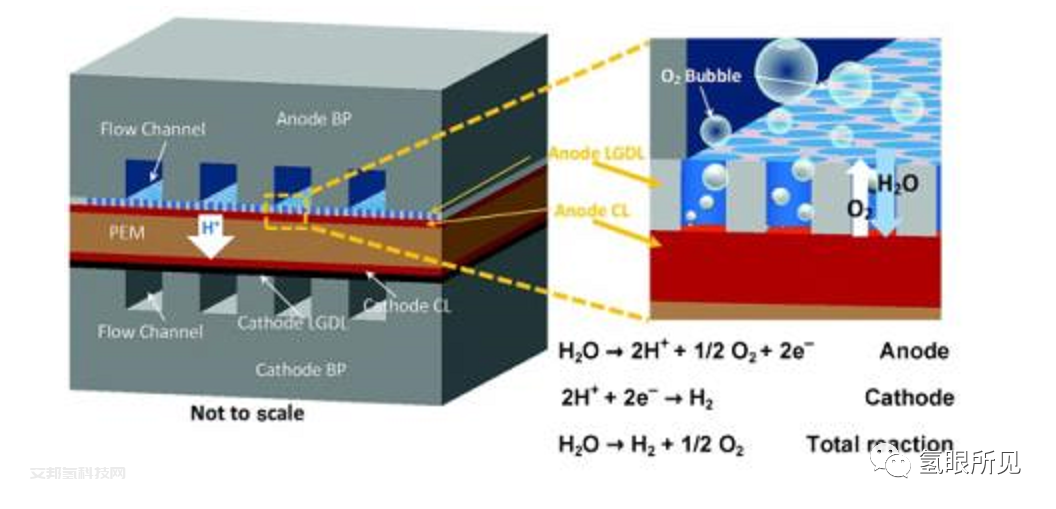
图8:薄钛GDL功能示意图。
(1)GDL必须耐腐蚀,这是由于阳极OER的高过电位、氧的存在以及水分裂过程中产生的质子所造成的高酸性环境。
(2) GDL需要导电,因此也必须具有良好的导电性和低电阻率。
(3) GDL还必须为膜提供机械支撑,特别是在操作压差的情况下,气体必须被有效地排出,水必须有效地逆流到催化层。
GDL通常由碳(如碳纸和碳布)或金属材料(如钛和不锈钢)制成。在这两种材料中,碳材料由于阳极氧化电位高,这使得碳材料易受腐蚀,另机械强度低,所以在PEMWE中只能作为正极。金属GDL由于其高导电性、快速生产和低成本而引起了人们更多的兴趣。即使在酸性和高阳极电位下,钛也是腐蚀性最小的材料,并且相对容易形成各种类型的多孔介质。因此,钛网/毡/泡沫/烧结粉末用作PEMWE阳极的GDL。目前对GDL的优化主要集中在对其孔隙和结构的调整。GDL的孔隙大小和结构对流体运移有很大影响。较大的孔隙促进了气体的去除,但降低了电子传输效率,减少了催化层中的水分。
相反,小孔隙阻碍了气体的排出,增加了传质阻力。因此,大多数研究的重点是优化GDL的孔隙结构,以获得良好的性能。Grigoriev等人通过实验和建模方法确定了GDL的最佳孔径、板厚和孔隙率。研究发现,最佳球粒径为50 ~ 75μm,最佳孔径为12 ~ 13μm。孔隙率应在30%-50%之间。传统的钛基GDL,包括毡、编织网或泡沫,具有纤维/泡沫孔隙形态,导致孔隙大小和分布随机。这种随机和非均匀的结构使得传统钛GDL无法精确控制液/气/电子/热分布。因此,人们迫切需要具有可调节和可控孔隙形态的新型GDL。Kang等人综合研究了具有直通孔和孔形态清晰的钛GDL(下图9)。他们的新GDL孔径为400μm,孔隙率为0.7,在80℃和1.66 V条件下达到了2A/cm2的最佳性能(见下图10)。薄且可调谐的钛基GDL显著降低了欧姆损耗和活化损耗,电催化性能远优于传统钛毡材料。他们发现孔隙度比孔径对性能的影响更大。利用高速微尺度可视化系统获得了电化学反应的直接可视化结果,发现气泡仅在孔隙边缘产生(见下图11),解释了孔隙大小和孔隙率对PEMWE性能的影响。
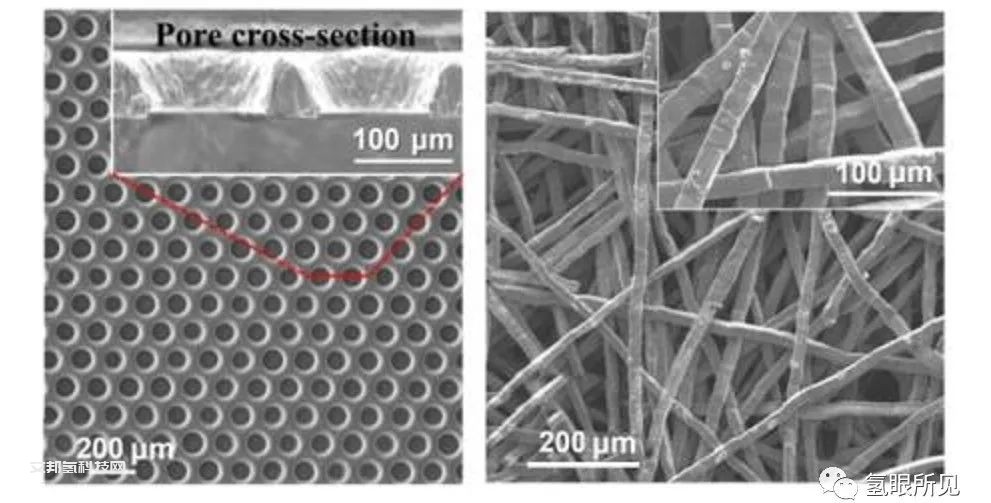
图9:扫描电子显微镜(SEM)图像的良好孔隙GDL和传统钛毡。
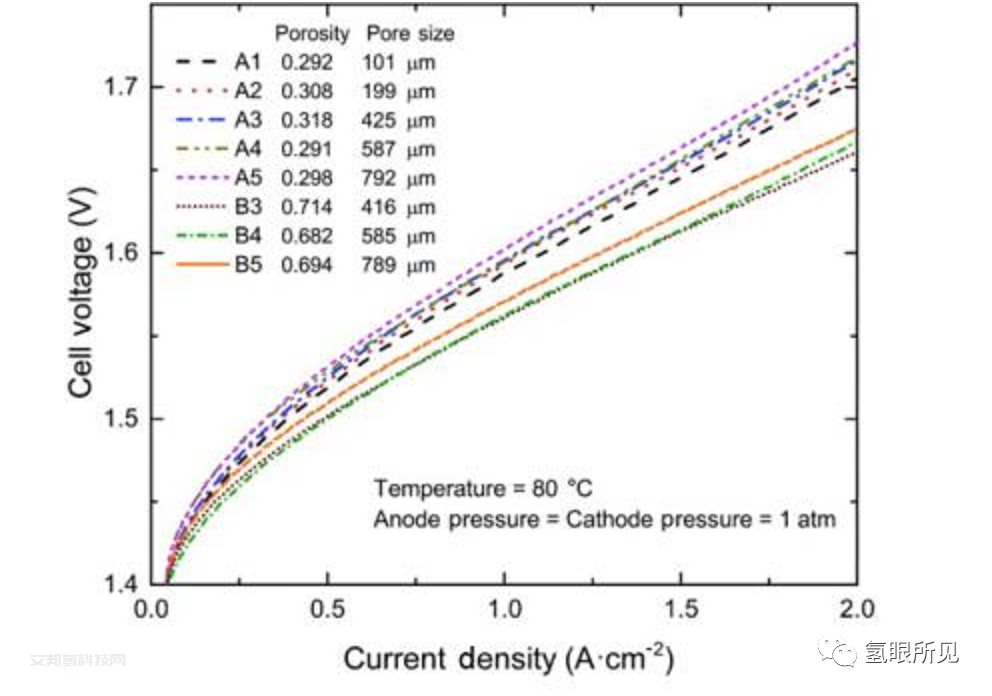
图10:不同GDL性能对比曲线。
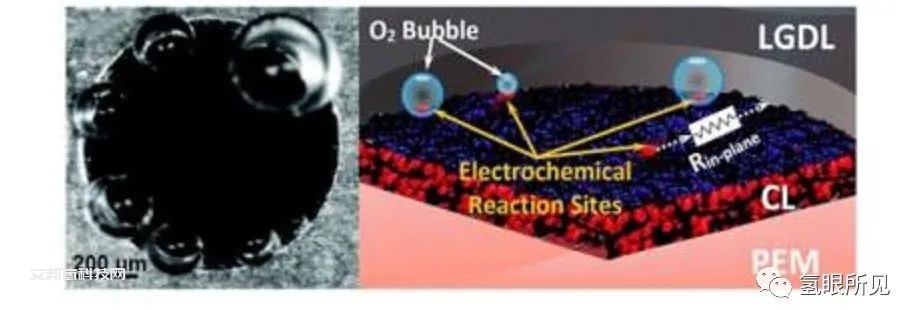
图11:可视化视频截图显示了一个孔内的电化学反应现象和示意图。
同时,GDL的耐久性和衰减也很重要。集电极降解一般可分为化学降解和机械降解两大类。化学降解主要是由腐蚀引起的,而机械降解主要是由压缩力、溶解和水热作用的侵蚀引起的。钛的降解主要是由表面钝化和氢脆引起的。钛在高电位、高湿度、富氧化环境中容易钝化,生成一层导电性较低的氧化膜,大大增加了钛与集液器之间的接触电阻。另一个问题是钛基材料最容易发生氢脆。因此,钛板通常涂有贵金属,如Au或Pt,以满足耐久性和性能要求,这也增加了其成本。因此,寻找低成本、高导电性、高耐腐蚀、抗氢脆的涂层材料是人们不懈的追求。GDL、BP和PEM以高压缩力固定在一起,防止水/气体泄漏。这种压缩力强烈影响GDL/催化剂层界面和GDL/BP界面的性能以及电解槽的整体性能。GDL在此压力下会发生一定程度的变形,表面不光滑会导致电流密度局部增强,影响器件的传质效率,降低器件寿命。光滑的液体收集表面对于减少接触阻力和防止降解至关重要。
四、双极板(BP)
BP是PEM电解槽中的多功能元件。BP有两个基本功能:一个是电连接堆叠中相邻的电池;另一个是供应和去除反应物(即水)和气态产物(即H2和O2)。其他函数包括质量传递函数和传热函数。这些功能必须在高压、氧化(阳极)和还原(阴极)条件下在电解槽的工作环境中保持。这些特性要求BP具有高导电性、耐腐蚀性、不渗透性、低成本和足够的机械强度。由于这些要求,没有太多的材料可用于PEM电解槽。目前,可作为BP的材料有石墨、钛、不锈钢等。这些双极材料都没有低成本的优点,都有各种操作缺陷。开发低成本和高性能BP对PEMWE的商业成功至关重要。
石墨因其高导电性而被用于燃料电池。因此,在制备PEM电解槽时首先想到了它。然而,石墨BP存在机械强度差、成本高、制造难度大、腐蚀速率高等问题。在阳极,高碳腐蚀降低了BP的厚度,这导致MEA和收集器之间的电接触电阻增加。此外,由于碳表面氧化,石墨BP的疏水性降低。这些影响导致BP的性能迅速下降,导致较差的寿命。石墨板只适用于阴极。为了解决这些问题,金属基板(如钛和涂层不锈钢)最近得到了研究。与石墨相比,钛具有优异的耐蚀性、低的初始电阻率、良好的机械强度和轻的重量,是目前PEMWE的最佳板材材料。但是钛板也会像GDL一样发生钝化和腐蚀现象。在高电位、高湿度、富氧化环境中,钛BP表面容易钝化形成氧化膜。具有低导电性的氧化膜大大增加了BP与集电极之间的接触电阻。研究了保护钛金属表面的涂层和合金方法。镀有贵金属或铂族金属,以满足高压和氧化环境下的耐用性和性能要求。例如,Jung等人使用镀金钛作为BP,并观察到由于电极与极板之间的电接触电阻降低,电解槽的性能得到了改善(下图12(a))。采用1μm金涂层作为阻挡层,抑制钛基板表面钝化层的形成。但是,BP涂层价格相当昂贵,特别是应用于大型电解槽时,不利于大规模的商业使用。因此,降低BP成本最有效的方法是通过改进涂层成分或制备工艺来降低涂层材料中贵金属的含量。
我们已经有了大量的钛的替代材料。不锈钢是钛的替代品之一,但不锈钢部件在恶劣的酸性环境中腐蚀反应非常快,因此还需要涂层保持合理的使用寿命。Yang等采用选择性激光熔化(SLM)印刷制备不锈钢板,然后镀Au表面处理,BP表现出良好的耐蚀性和电子导电性。Gago等人采用真空等离子喷涂(VPS)在不锈钢衬底上制备了致密钛涂层。然后通过物理气相沉积(PVD)磁控溅射沉积Pt,进一步对Ti涂层进行表面修饰(下图12(b))。致密而坚固的钛涂层提供了必要的保护,防止不锈钢表面的点蚀。在PEMWE中找到了低成本的钛双极性涂层/表面处理解决方案,包括氮化涂层和铌涂层。除涂层处理外,整体单元的设计也是研究的重点。Yang等人利用增材制造技术制备了具有高度复杂内部结构的多功能集成PEMWE单元,从而大大提高了性能(下图12(c)和(d))。这是PEMWE组件首次被集成到一个单板中进行水分解和制氢。薄板的结构创新为PEMWE的简化提供了突破性的发展,从而大大减少了其部件的数量和重量,为PEMWE的优化配置提供了机会。
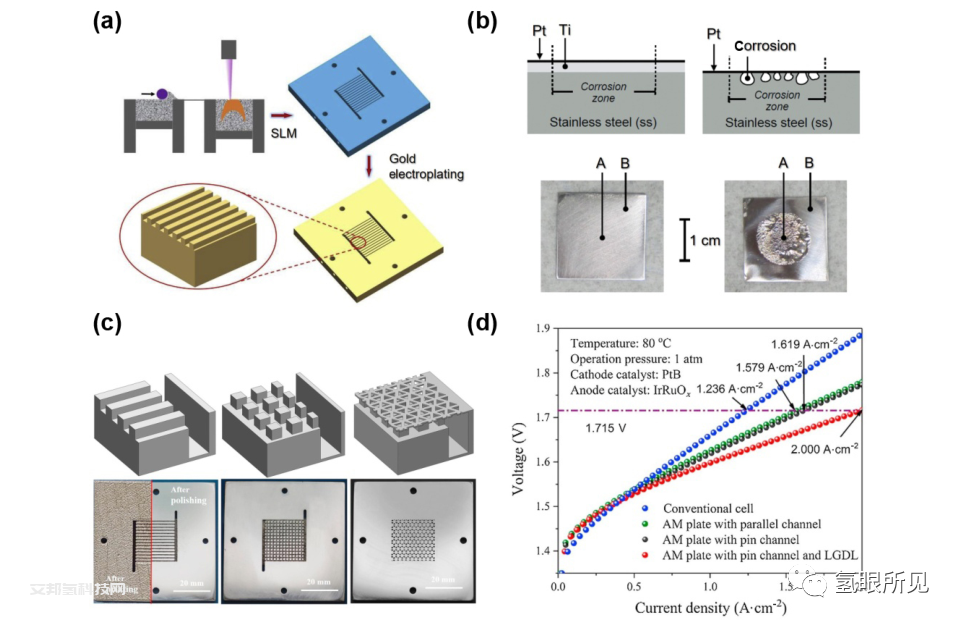
图12:a)镀金不锈钢bp的制造工艺:(b)在不锈钢上沉积Pt/Ti和Pt涂层的方案和腐蚀试验后Pt/Ti/不锈钢和Pt/不锈钢的照片。(c)平行流道、引脚流道和带GDL引脚流道。(d)不同阴极板的PEMWE极化曲线结果。
流场也是BP的组成部分之一,流道通常刻在BP上。其具体功能之一是产生在催化电极上均匀分布的流场。流场板表面积上的不均匀流动分布可能导致珍贵催化剂材料的不均衡使用,装置的整体效率低于预期。因此,必须正确设计电解槽的流场板,使反应物(水)均匀分布在催化反应表面,提供一种收集反应产物(氢和氧)的途径,并提供通往反应现场的导电路径。对于大面积电解槽,流场的作用尤为重要,而流场设计不合理往往是电解槽性能下降的主要原因。目前,研究人员已经设计开发了多种流场结构,如点流场、多孔流场、蛇形流场、组合流场结构等。在PEMWE中,流场的形状和几何形状直接影响着反应物分布的均匀性和流道的热管理效率。Toghyani等研究了PEMWE的五种流场设计(下图13(a) - (e)),包括平行流场、单路蛇形流场、双路蛇形流场、三路蛇形流场和四路蛇形流场。结果表明,由于氢摩尔分数和电流密度分布更好,单路径蛇形图的性能最好(图13(f))。此外,Li等人通过实验研究了高温下流场对PEMWE性能的影响。结果表明,阴极流场模式影响欧姆过电位,阳极流场模式影响活化过电位。
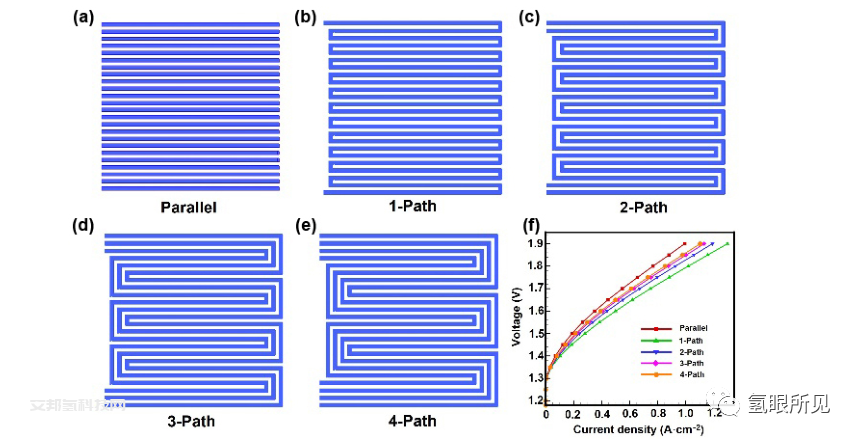
图13:(a) - (e) PEM电解槽内不同流场示意图。(f)不同流场形态下阳极侧出口流道的极化曲线。
总结:
MEA(含工艺)、GDL、BP占据了PEM电解槽的90%的成本,PEM的降本必须从这几个主要部件着手去改进,更低价耐用的材料和工艺都需要突破,同时还需要兼顾性能。当然除了这些之外,约占槽体成本10%的边框(Gasket)和密封部件也需要有个更合理的设计方案!
原文始发于微信公众号(氢眼所见):PEM电解槽关键材料综述